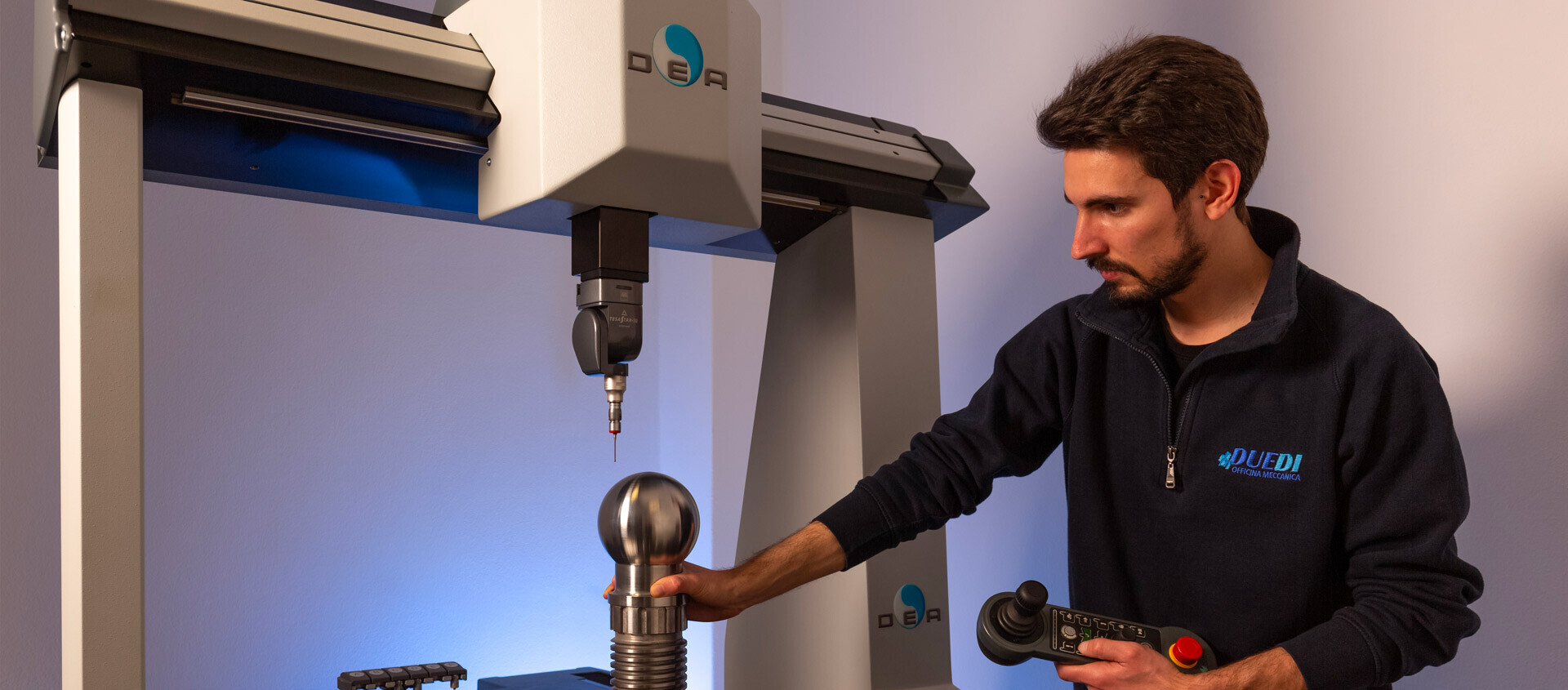
Quality
DUEDI always gives great importance to the quality of the products supplied to its customers.
To make this possible we have set ourselves the task of providing material certifications, post-processing dimensional tests, non-destructive testing reports, and welding quality tests to all customers who wish.
All these certifications are obtained through cutting-edge control systems and partners consolidated over the years.


Our material certifications
For all the material that DUEDI purchases and which is then used for the production of the various components, a certification is issued according to the UNI EN 10204 standard.
All our suppliers are able to issue us:
Declaration of conformity
Declaration of conformity of the material by the manufacturer without data regarding laboratory tests (chemical analysis of the casting and mechanical tests)
inspection certificate
The material is defined as compliant based on tests carried out on products of the same type (non-specific control).
declaration of conformity
declaration of conformity of the material by the manufacturer based on tests carried out on samples of the same casting, from the same batch. The document is issued by the company's internal quality manager (specific control).
test report
Manufacturer's declaration of conformity based on tests carried out on casting and batch samples verified and certified by a third party.
Among these, the most requested certification is 3.1 as its purpose is to guarantee complete traceability of the material.
Non-destructive check and welding quality tests
Non-destructive checks are a complex of examinations, tests, and surveys conducted using methods that do not alter the material under examination in any way and are often also used to test the quality of welds.
These do not require the destruction or removal of samples from the finished piece and are aimed at finding and identifying defects in the piece itself. The acronym NDT, derived from the English Non-Destructive Testing, is often used as an abbreviation.
In the industrial sector, this type of testing is required for all critical details that must be checked to verify their integrity and compliance with current regulations.
The main non-destructive testing methodologies we propose are:
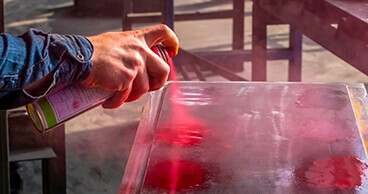
are based on enhancing the visibility of open surface defects using a substance that penetrates the defects by capillarity (penetrant liquid) and a background (detector).

technique that uses high-frequency acoustic waves to detect internal defects.

is based on the attraction of ferromagnetic particles dispersed in liquid which are then attracted by the magnetic field dispersed near any cracks.
Dimensional testing
Dimensional testing is an indispensable part to be included in the production process of the finished product. This certifies that all the "critical" measurements with precise tolerances to be respected comply with what is specified in the drawing and/or in the design phase of the part.
To achieve this objective DUEDI uses a Hexagon DEA Pioneer gantry. It is used for the qualification of auxiliary equipment, for process control, and for the control of input/output details. It turns out to be a reliable control system for dimensional control of both mechanical components and prismatic details. Measuring range: X=800 mm, Y=1200 mm, Z=600 mm
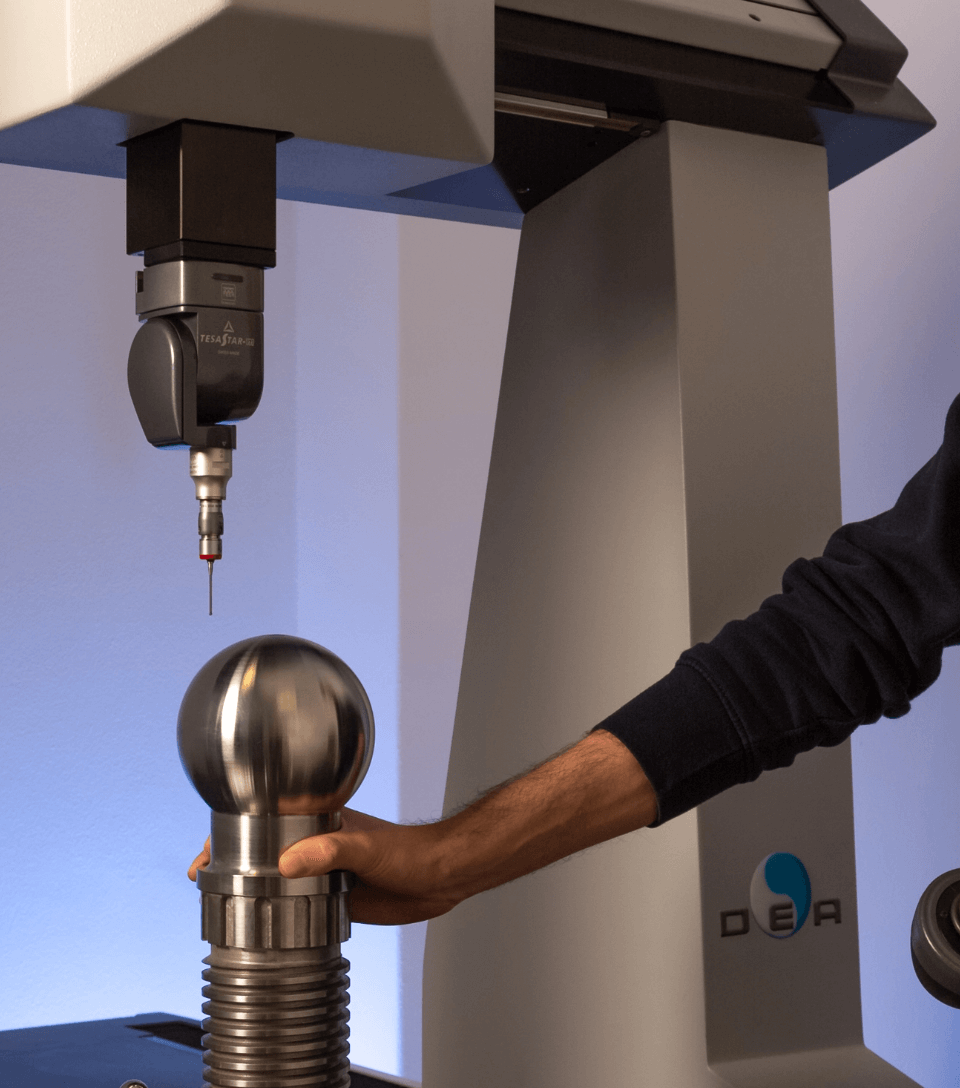
Component marking
Precisely in response to the need to have the traceability of materials and finished parts, DUEDI uses a Sitel MK3 pneumatic marker with which it is possible to carry out any marking using a punch.
We are often asked to mark data such as orders, codes, order references, progressive numbers, dates, logos, etc. both on small components and on carpentry or details with considerable dimensions.
This procedure does not damage or alter the composition or quality of the material in any way.
